-
the Worlds Top Performers
Tooling
Aerospace & Power Industry
Oil & Gas, CPI & Renewables
Industrials
voestalpine BÖHLER Bleche
Materials forthe Worlds Top PerformersToolingAerospace & Power IndustryOil & Gas, CPI & RenewablesIndustrials
For the Worlds Top Performers
For generations, the name BÖHLER has been synonymous worldwide with special steel of the highest quality. Our customers are leading companies in future-oriented industrial sectors and highly innovative specialists who push the boundaries of what is possible with their solutions. The new stainless steel plant secures this leading position for future generations.
Our products at a glance / An overview of our products
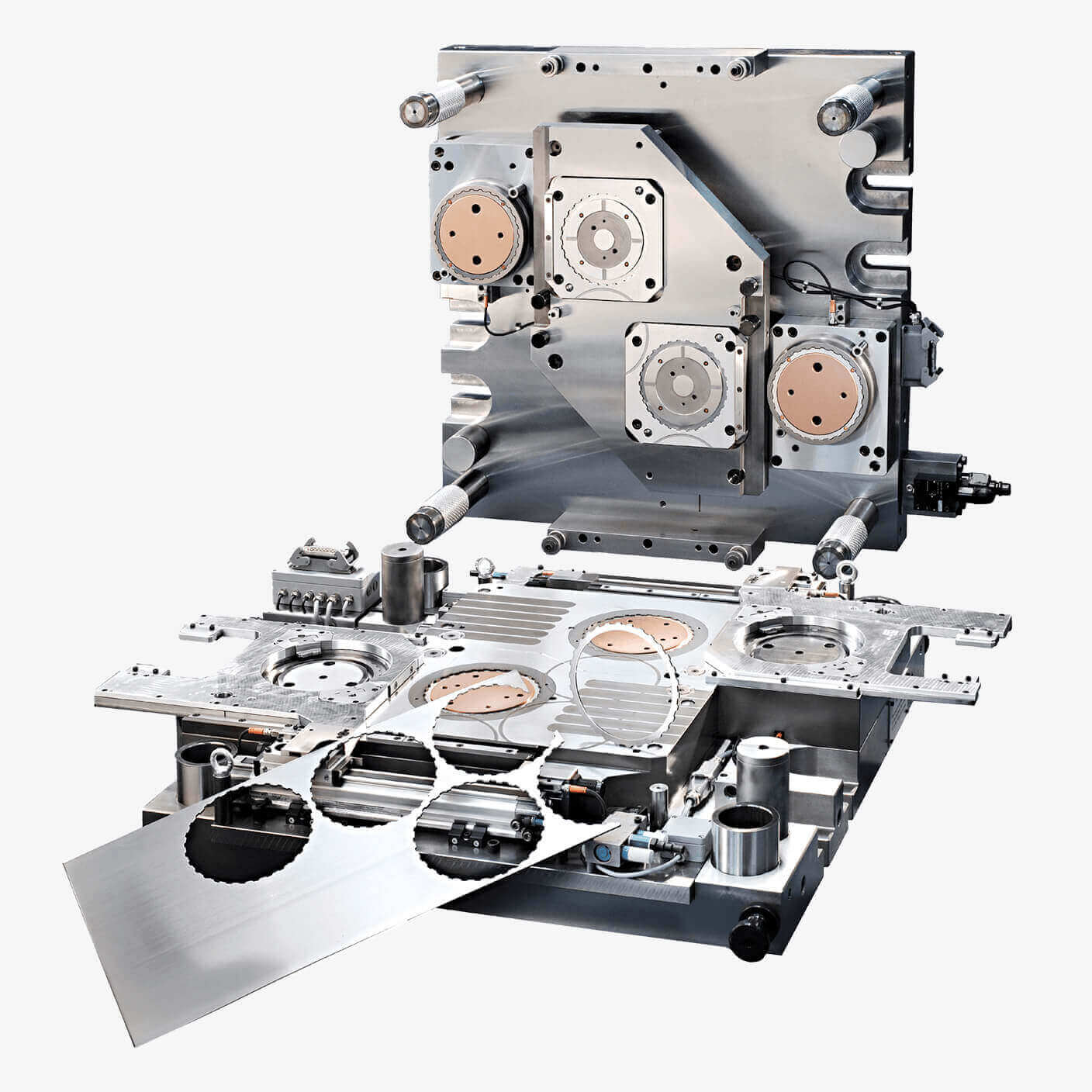
Cold work tool steels
Cold work steels are mainly used in cold forming tools. Hardness, wear resistance, toughness, compressive strength and fatigue strength are achieved by alloying with Carbon and Chromium, Tungsten, Molybdenum, Vanadium and Manganese. Hardness values of 50 to over 64 HRC are achieved by hardening and tempering the tool components.
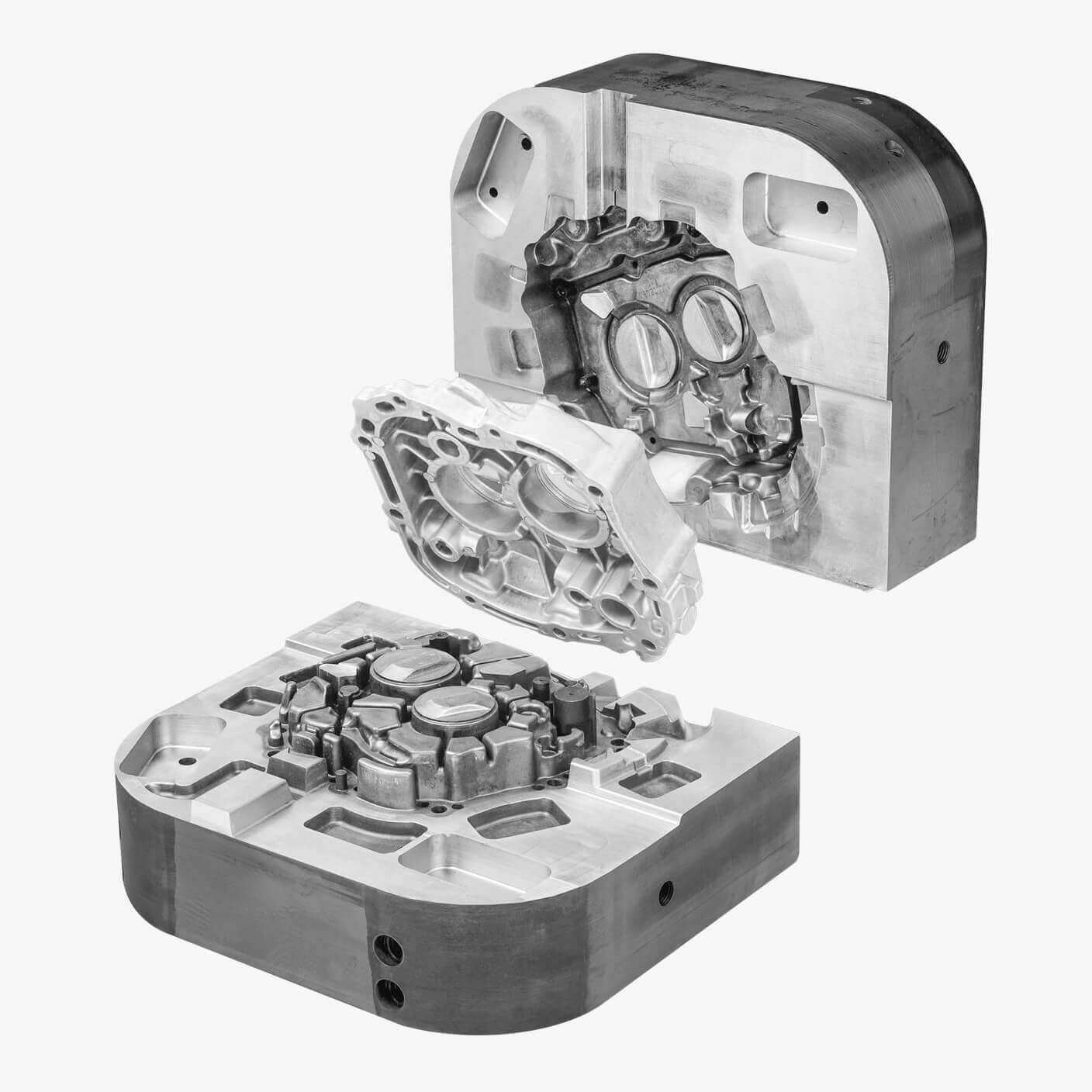
Hot work tool steels
Tools for hot forming processes require fracture resistance, hot wear resistance and resistance to thermal fatigue. Tempered 3% and 5% CrMoV steels with a hardness of approximately 35 to 55 HRC fulfil these requirements perfectly. Particularly highly stressed tool inserts are also manufactured from maraging steels of the type Fe-18% Ni-Co-Mo-Ti.
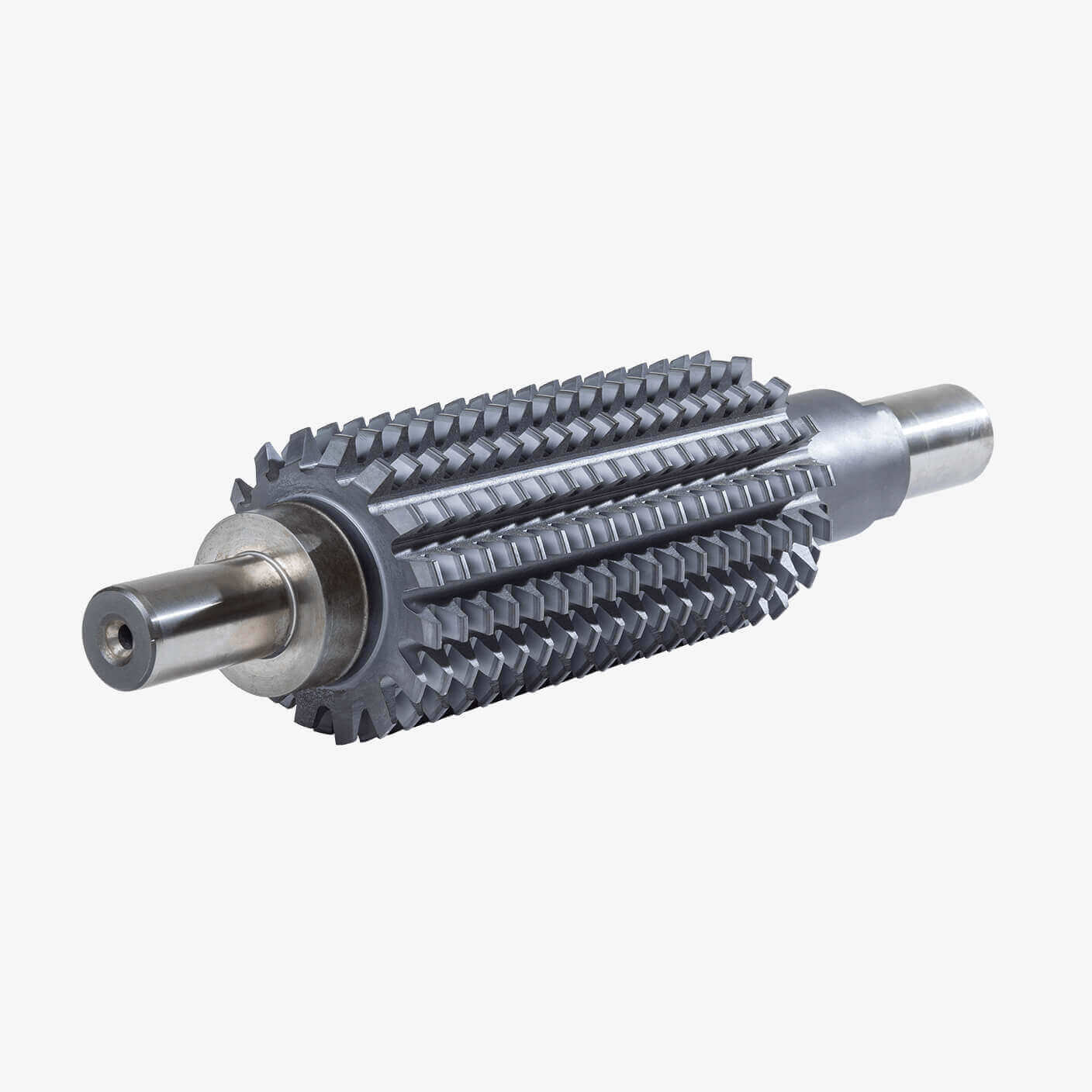
High speed steels
Cutting tools made of High-Speed Steel achieve high hot hardness, wear resistance and fracture resistance at a hardness of over 60 to 67 HRC through hardening and tempering. The main alloying elements are Carbon, Tungsten, Molybdenum, Vanadium and Cobalt. High contents of carbide-forming elements lead to the formation of wear-resistant carbides in the microstructure.
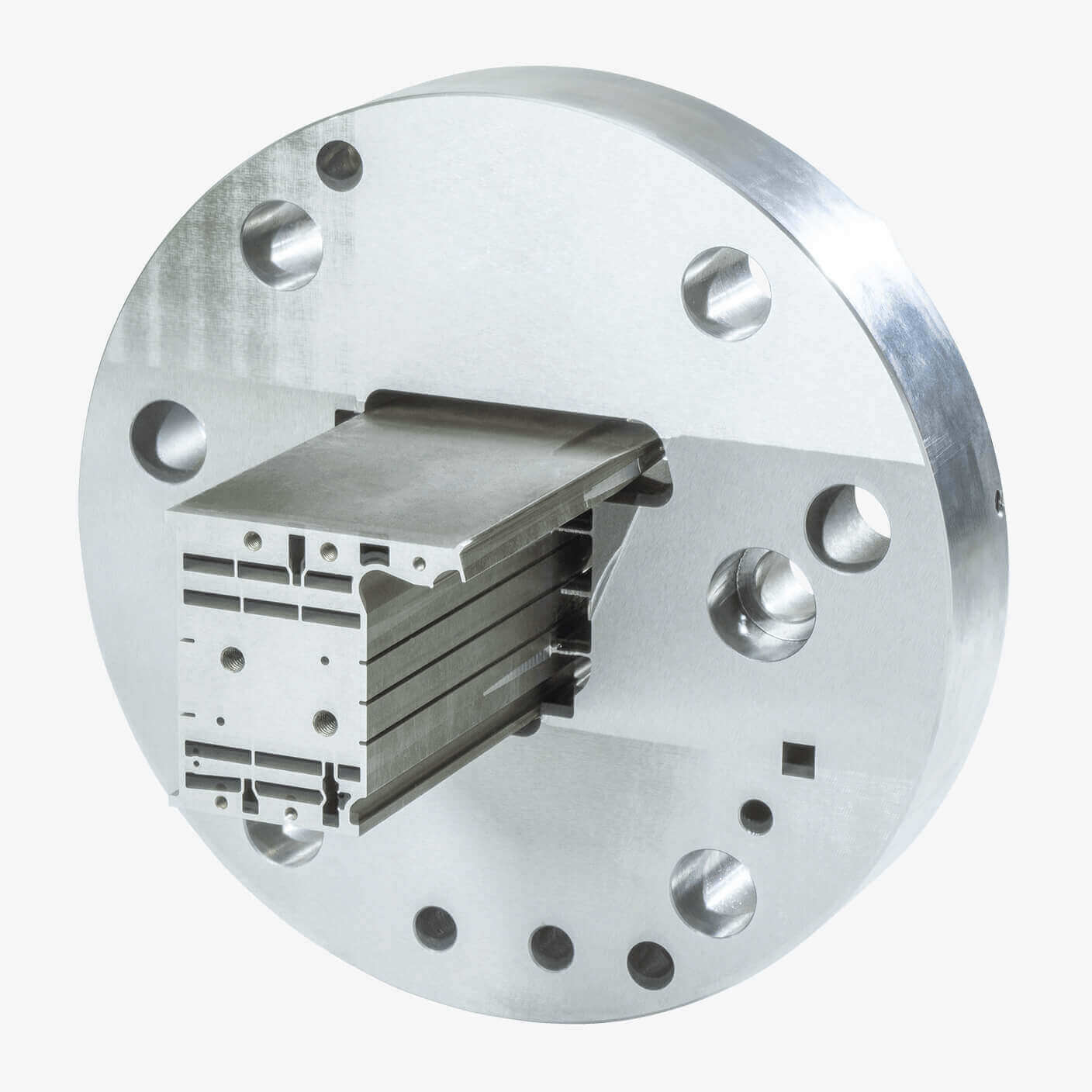
Plastic mold steels
The requirements for mould steels are more diverse than in any other manufacturing process. Wear resistance, especially when processing fibre-reinforced plastics, and in addition corrosion resistance, machinability, polishability, thermal conductivity and mechanical properties are among the most important criteria.
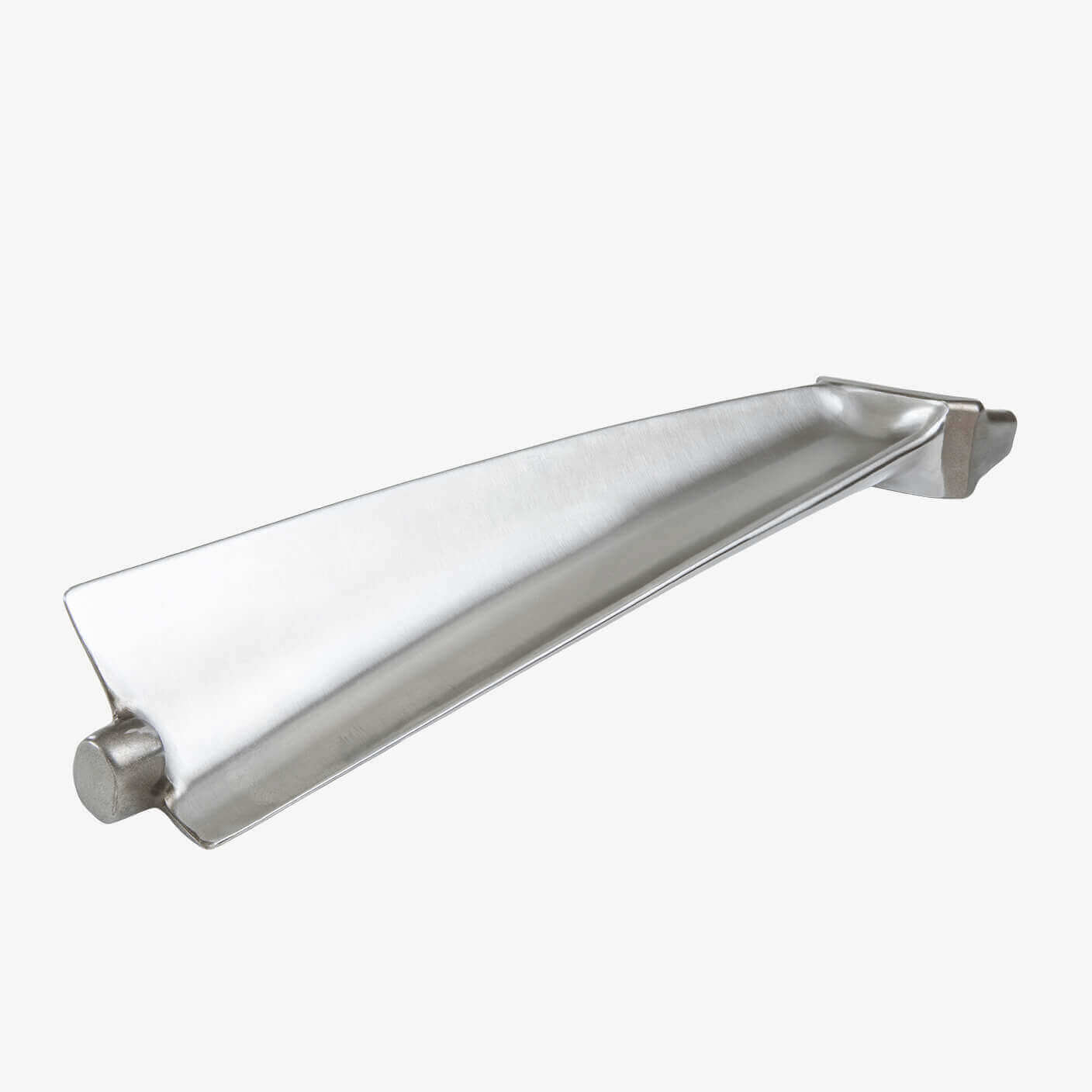
Ni-Base alloys
Nickel-based alloys are used as high-temperature and chemically resistant materials. The chemical resistance is primarily determined by the alloying elements Chromium, Molybdenum and Tungsten. Maximum thermal resistance can be achieved by precipitation hardening with Aluminium, Niobium and Titanium.
-
Cutting Tools
Cutting processes, e.g. drilling, milling, threading or broaching, require tools made from selected high-speed steels. BÖHLER high-speed steels optimally combine the required properties such as high edge retention, hot hardness and toughness. For our customers, this means reliable and reproducible production processes, long tool life and lower set-up costs. -
Aerospace
The aviation industry demands reliable materials for airframes, engines and landing gears. BÖHLER produces and supplies steels and alloys according to given specifications and standards, in the desired composition and dimensions with the desired properties. Every single production and testing step is in our hands and ensures quality at the highest level -
Hot Work
BÖHLER hot-work tool steels are mainly used in highly stressed forging and die-casting tools and, due to their good combination of properties, also in cold work and plastics processing. The main focus is on offering customized material solutions with high-quality, remelted steels. -
Oil & Gas / CPI
Safety-related and economic challenges in these segments demand a wide range of properties from the materials used. The product portfolio includes proven, highly corrosion-resistant steels and alloys of high quality. Voestalpine Böhler Edelstahl is a fully integrated manufacturer of nickel and steel alloys for these demanding industries. -
Automotive
The automotive product portfolio includes soft magnetic materials, high-performance case-hardening steels as well as High Speed and hot-work tool steels. BÖHLER produces and supplies highly functional materials, primarily for the highly stressed powertrain area and for injection components under high quality and product safety standards.